News |
Featured:
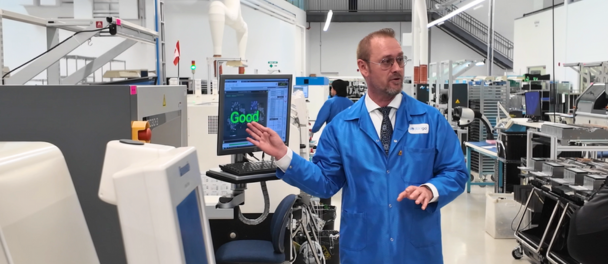
7 Key Files to Share with Your Electronics Manufacturer
In electronics manufacturing, many of the most common delays can be traced back to gaps or ambiguities in documentation. Even with a highly experienced manufacturing partner, a successful build depends on clear and detailed communication. When there are misalignments...
All News:
7 Key Files to Share with Your Electronics Manufacturer
In electronics manufacturing, many of the most common delays can be traced back to gaps or ambiguities in documentation. Even with a highly experienced manufacturing partner, a successful build depends on clear and detailed communication. When there are misalignments...
Pioneering Electronics Manufacturing for a Healthier World
Whether you are manufacturing electronics to support people’s health, or keep the environment healthy, our expertise helps bring your innovative products to market.
Unlock the Future of the Canadian Electronics Industry with the 2024 Canadian Electronics Industry Report
Download the 2024 Canadian Electronics Industry Report now.
36,070 Feet Below the Ocean
Kongsberg Discovery and Dorigo Systems Deliver Exceptional Performance in Extreme Environments
Join Us at EPTECH Mississauga on October 16th
Stop by and find out why we’re part of something extraordinary!
Dorigo Systems Ranked 49th in BIV’s “2023 Top 100 Technology Companies in B.C.”
Dorigo Systems has been included in the 2023 Business in Vancouver list of 100 top tech companies in B.C. These much-anticipated annual rankings show which tech companies are growing in B.C.
Case Studies:
Do You Have a Safety Net in Manufacturing?
What’s key to bringing innovative products to market in a cost-effective and timely manner?
Disrupting Fleet Management with Made-in-Canada IoT Innovation
Knowing where fleet vehicles and drivers are at all times identifies potential problems sooner and mitigates risks before they become larger issues that can impact driver safety or increase operating costs.
Building Higher Quality Electronics through Outsourcing – North America or Offshore?
Outsourcing design and manufacturing is a cost and resource efficient approach to product development. In fact, Dorigo Systems is one of the Pacific Northwest’s leading contract manufacturers of Printed Circuit Board Assemblies (PCBA) and the preferred choice of OEMs.
How to Deliver “Copy Exact” Precision Measuring Sensors with 100% On Time Delivery
In an industry where dollars saved in manufacturing is a measure of profitability, time is money. Having the right manufacturing partner brings everyone success.
Dorigo Systems Ltd.
5085 North Fraser Way
Burnaby, BC V5J 0J2
Canada